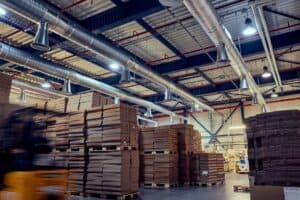
Image credits: Airlogix
Temperature control is a primary management aspect for all warehouses. Since the vast, generous interior space is ideal for commercial and industrial uses, it is important to ensure optimum temperatures for both the stored goods and the employees who work there. Heating and cooling such an area can be quite expensive, especially if there are specific temperature controls for each inventory type. Your overall warehouse HVAC costs can be split into your choice of HVAC units, installation costs, and ongoing maintenance – all of which contribute to a fully functional HVAC system. In this article, we will browse through some average costs and discuss how to keep your numbers as low as possible while maximizing the HVAC output.
Warehouse HVAC costs
On Average
The cost to heat or cool a warehouse is generally high in terms of energy consumption and maintenance – considering the total square footage that needs to be heated or cooled. All of this massive space can actually be divided into the usable square footage that requires HVAC systems and the remaining square footage that is mostly idle or unoccupied. So, there is always some energy loss associated with warehouse HVAC systems because of the amount of space we are dealing with.
In general, warehouse HVAC costs take up around 30% of the total operational costs required for a warehouse. The more specific and complex the requirements, the higher the costs – and this entirely depends on your intended commercial or industrial expectations for the available space. Usually, warehouse types can be categorized into a general storage warehouse, a cold storage warehouse, and an office warehouse – so your total costs will differ according to your specific application.
Following an example from Strong Building Systems, let us look at some average numbers for a 5000-square-feet warehouse, which is typically the ideal size for small and medium commercial purposes. Small warehouses tend to be categorized as shell structures because of their basic spatial arrangement that does not include lighting or HVAC, so they cost around $19-$25 per square foot during construction. In comparison, if the warehouse HVAC and other key amenities are included, you will be working with a construction budget of $55-$70 per square foot. Therefore, you can expect your warehouse plus HVAC construction costs to range between $275,000 to $350,000 in total.
Influencing Factors
Apart from the size of the warehouse itself, various factors can affect your total HVAC costs. For example, cooling systems rely on different refrigerants that need to be compatible with your choice of HVAC pipes. You also have to consider if the refrigerant is harmful and requires professional handling and safety gear – all of this will increase your total warehouse HVAC costs. Material compatibility, suitable insulation, flammability risks, and personnel training are all essential cost considerations for anyone running and managing a warehouse.
Similarly, HVAC specifications that are more demanding and technical in nature will add to your overall costs. This is particularly true for cold storage warehouse systems that have heavy-duty expectations for their cooling and ventilation units. They also rely on a backup power supply that can seamlessly resume the cooling process in case of a system failure – which is exactly the kind of risk you should be prepared for while storing perishable goods. Therefore, setting up the HVAC infrastructure for such warehouses is generally quite expensive.
Cost Breakdowns
Your warehouse HVAC team will include specialized HVAC estimators apart from installers and maintenance experts. Before finalizing your budget, make sure to request detailed estimates to understand the general breakdown of your warehouse HVAC costs. Such a cost breakdown usually includes elements like:
- Digital takeoffs for your HVAC systems
- Materials and associated quantities
- Vendor pricing
- Hardware, equipment, and fixtures such as pipe fittings, ducts, hangers, elbows, and similar accessories
- Labor charges
- Permit charges
- Costs for drawing plans and HVAC layouts
By receiving itemized quotes, you can compare your selected bids more efficiently and understand how much value is added per square foot of your warehouse. Cost breakdowns are also useful for finding out how different materials and hardware compare depending on your applications, expected loads, safety aspects, and warehouse compatibility. They also highlight the permit charges you will most likely incur, so this will be a great opportunity to confirm a code-compliant project regardless of your new construction or renovation needs.
Ways To Bring Down HVAC Costs
Don’t Delay The Stitch In Time
Routine maintenance programs are crucial for the efficiency and operability of your warehouse HVAC systems. If you want your expensive setup to last longer, it is important to schedule preventive maintenance down the road with your HVAC contractors. This includes checking for leaks, replacing damaged parts, cleaning or replacing filters, cleaning all the vents, removing debris buildup, and so on. Dust and debris buildup will not only cause mechanical wear and tear, but it will also leave you with an overworked HVAC system that is bound to collapse.
By investing in scheduled maintenance programs (say at least $50 or so per month depending on your HVAC performance), you can allow your HVAC infrastructure to stay updated, which prevents the chances of system failures, business downtimes, and hefty losses such as inventory damage. After all, a stitch in time saves nine!
Watch Out For The HVAC Enemy: Leaks
Leak detection is a key aspect of all HVAC maintenance programs, so we decided to give it the undivided attention it deserves. Some common sources of HVAC leaks include damaged ductwork, frequently opening and closing doors/windows, a lack of insulation, and broken connectors. By inspecting your HVAC ductwork regularly for leaks, you can address energy efficiency issues that you might be facing – as leaks are the root causes of inadequately heated or cooled warehouse interiors. If you notice that your warehouse temperatures are suspiciously different, it means that your HVAC systems are not performing to the best of their potential, and this is your cue for a thorough leak inspection. It can be difficult to conduct leak inspection and detection considering the large scale of a warehouse structure, which is why this area of maintenance can be costly – but definitely not costlier than the high energy bills you will otherwise pay.
Even though all of the vast warehouse space increases the scope for leaks, there are basic preventive measures you can take to overcome this problem and retain the heating or cooling more efficiently. For example, you can enhance your warehouse’s temperature control by sealing off known leaks and investing in proper insulation barriers. This also depends on the number of doors and windows your warehouse has. Each time you open a door or a window, you compromise the ambient heating or cooling levels because all of that built-up climate quickly escapes the warehouse. This causes your HVAC systems to go on a repetitive loop trying to compensate for the lost air – which is not very energy efficient. Therefore, to preserve your HVAC integrity as well as your warehouse HVAC costs, consider installing quick-close doors that seal properly and use vinyl curtains as an extra barrier.
Help Your HVAC Get Smart
It is never too late to switch to automated controls, and in the spacious world of warehouse HVAC, automation will be your best choice for keeping the costs down.
For example, you can use sensors and smart thermostats to automate schedules and HVAC cycles depending on occupancy and other applicable factors. In this way, your installed units will only work when needed and automatically switch off once the desired temperatures are achieved. Compared to units running 24/7 in a warehouse, this is a much smarter way of regulating the indoor climate and automatically turning off the system when it is not needed – which also gives the individual units more time to rest, and this extends the overall lifespan of your warehouse HVAC.
Warehouses can immensely benefit from zoning as well. By creating smart zones within your warehouse space, you can decide which areas require dedicated heating or cooling and which areas have more flexibility in terms of temperature controls. Zoning can help you set individual climates for both high-traffic areas as well as inventory-specific areas that need a strict temperature regulation to preserve the goods. Automation technologies allow businesses to plan their HVAC allocations more effectively and avoid wasteful consumption, so you can never go wrong by updating to smart controls and zones – especially if you are already updating an old HVAC infrastructure from scratch.
Conclusion
Planning energy-saving strategies can help you manage your warehouse HVAC costs better and be more conscious about the ongoing performance. This is why preventive maintenance should be discussed as part of your initial HVAC consultations with estimators and contractors. Instead of pushing routine inspections to the end, you should make sure that you hire contractors who also offer future maintenance services and take the effort to break these down early on during cost allocations. In this way, you will have both a current budget to work with and a clear idea of how much future expenses you can incur during your HVAC’s lifespan.